Сustomer company (information about company is under NDA) is an international company that develops and manufactures intelligent fluid flow equipment. The company has more than 1000 employees on all continents and is one of the leaders in its area.
When the customer turned to NetLS, the project had separate modules for different countries due to different measurement systems and technical marking of the product (different standards).
For example, motors for the American market are using NEMA standards, using horsepower to measure power and have their own separate power scale. The other part of the world uses the IEC system, labeled in kilowatts and other power standards.
The general modules (e.g. the sales module) were very difficult to maintain and process. As a result, there were widespread problems that are difficult to notice in the reporting, as well as a significant error in the calculations (the error was 5 times greater than if everything was built in one system). Engineers in different countries used different measurement systems and different standards, even when they were in the same department.
Accordingly, communication was complicated and ineffective.
To resolve this issue, our team has developed a system consisting of 3 modules.
Principle of operation
The user enters input data into the system (for example, in the English system of measurements). Then module 1 converts all incoming parameters to the metric system and passes them to module 2.
Module 2 performs all calculations in a single measurement system.
Further, this module sends the received data (results) to module 3, which, in accordance with the user's standards settings, selects the necessary product and returns its technical characteristics to module 2 in a single measurement system.
Module 2 processes the returned features, generates graphs, checks the requirements of the standards, and returns the result to module 1.
Finally, module 1 converts the results to user measurement units.
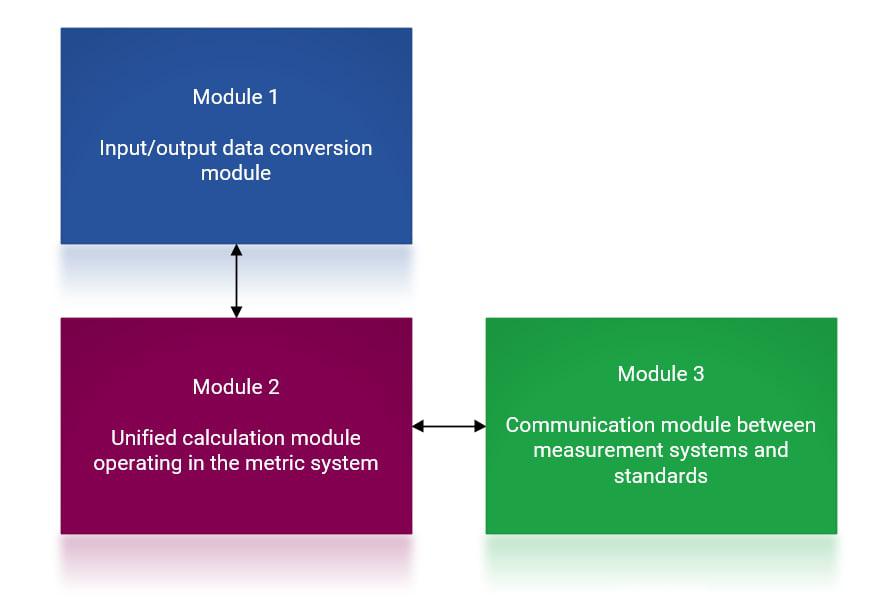
Example
A pump must supply water to extinguish a 1000 sq. ft. fire and the user selects the United States as the installation country.
Module 1 converts the information to the metric system of measurements. Module 2 performs additional calculations (e.g. how much water should be applied to extinguish a fire in a given area of ignition) and determines that the minimum power is x kilowatts. Module 2 then sends this information to module 3, along with information about the need to use US standards.
Module 3 knows that according to US standards, the required minimum headroom is 10%. The module selects the motor in horsepower and transmits its characteristics in the metric system of calculations. The name and nomenclature of equipment remains the same.
Module 2 then continues the calculation and module 1 displays the results in the original units.
By converting all input to the metric system, all data is stored in a single measurement system, which makes it possible to get rid of large errors in multiple conversions and avoid formulas using mixed and non-systemic units (like pressure in bars or using horsepower and liters simultaneously).
With the help of a unified system, communication between departments has become more efficient.
The system increased the efficiency of management and planning of the factories, which made it possible to sell products, reducing the amount of idle stock in warehouses on average by 7%.
In turn, as a result of the introduction of a universal system, the productivity of a sales manager increased by 5%, and the time for training a manager was reduced by 40%.